Dive Brief:
- Amazon plans to convert more fulfillment centers to only handle paper packaging that is widely recyclable in curbside programs — no plastic packaging — following the rollout of its first such facility earlier this month near Cleveland. It will use data gathered during continued testing at the Euclid, Ohio, facility to influence which fiber-centric systems get installed at other facilities.
- The Ohio fulfillment center upgrade focused on two main technologies: a retrofit to equipment that previously made plastic mailers and now produces unpadded flexible fiber packaging, and a new technology: a right-sized box-making machine.
- Amazon also developed a stretchable paper to use in the retrofitted bag-making machines. The paper’s coating gives it more pliability than a standard paper bag and heat-seal capabilities without affecting recyclability, which is important because “curbside recyclability is a critical element of switching to paper,” according to Pat Lindner, vice president of mechatronics and sustainable packaging at Amazon.
Dive Insight:
Amazon is just coming off a round of “Prime Big Deal Days” earlier this month, which spurred a spike in orders. The increased orders should continue through the holidays, Lindner suggested, which makes now the perfect time to test the new automated systems.
“When we test technology, we want to make sure we do it in the toughest of circumstances. ... That was one of our motivations of starting earlier in the year: I really wanted this technology to run through our busiest time,” he said. “That will also have a big impact on the confidence we have to bring that technology to other sites.”
Amazon chose the Euclid site for its first 100% fiber-focused fulfillment center because it’s a large, well-established operation that ships to a lot of different regions, Lindner said. Although potential locations and the timeline for converting other facilities is uncertain, “given the size and the complexity of our network, it most certainly will be a multi-year effort,” he said.
While introducing a new technology typically results in “a little bit of a [production] dip,” the Euclid plant now is at full capacity, Lindner said. Amazon owns the intellectual property to both new systems installed in Euclid, he said.
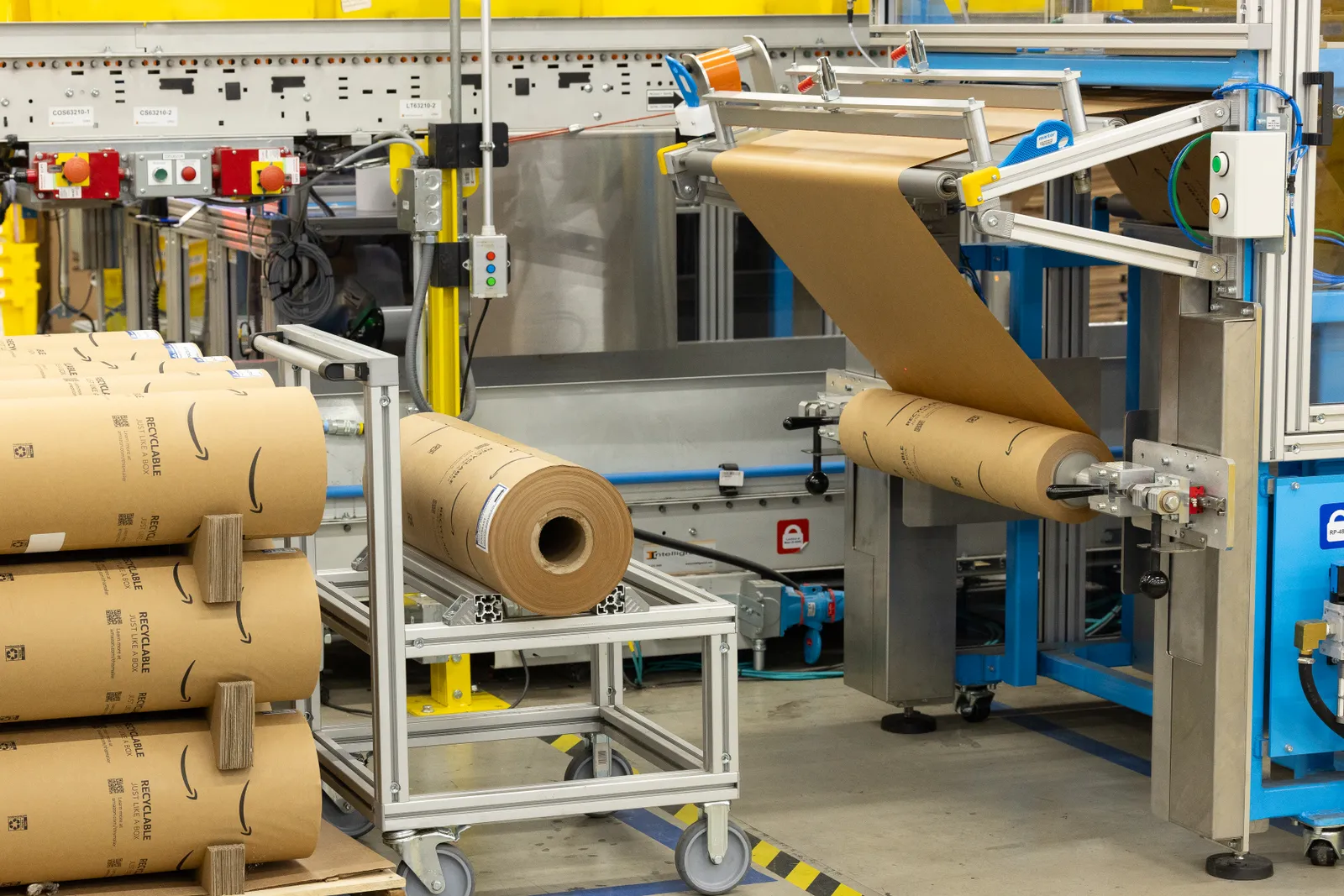
The retrofitted equipment that produces unpadded fiber mailers contains a sensor that identifies the right packaging size for each product. Its heat-sealing technology ensures the product is fully protected during transport. Plus, the stretchable paper is reportedly more weather resistant than standard paper bags.
Products packaged in the right-sized box machinery require more protection than the unpadded bags. The automated equipment measures a product’s dimensions and folds the corrugated material around the product. The material is more flexible and lighter than standard boxes.
The facility transformation is part of Amazon’s broader effort to reduce plastic and cut packaging waste to improve sustainability. The company recently stepped up its ships-in-own-packaging program as another key tactic.
“From our strategy standpoint, the first thing we want to do is eliminate packaging wherever we can. Second is we're going to move to paper. And then third is wherever possible to automate that technology,” Lindner said.
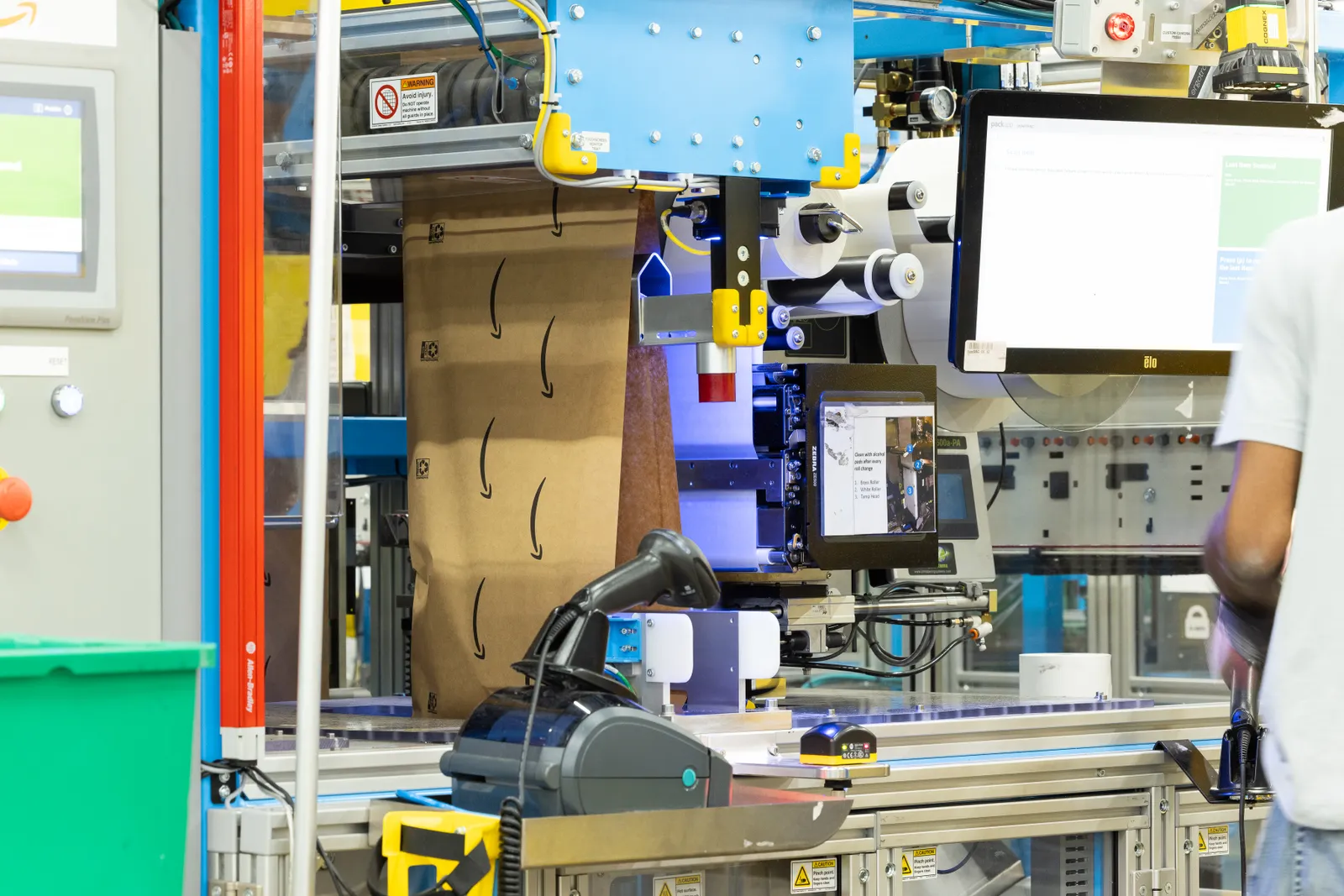
Adding more automation affects employees at the facilities. As employees train on the new technology and the automation boosts efficiencies, workers can “take on tasks that are more rewarding to them,” Lindner said.
As speakers repeatedly said at the E-PACK conference in Chicago in early October, competitors tend to follow the paths that Amazon trailblazes. Therefore, it would not be surprising for other big e-commerce players to soon consider, if not embark on, similar fulfillment center conversions. Earlier this year, Walmart announced it would switch to fiber mailers and right-sized boxes to cut packaging waste.
Correction: This article has been updated to clarify the name of Amazon’s recent Prime sales event.