Last spring, A1 Organics, Colorado’s largest composter, drew a line in the sand, or, in the compost.
In April, the company said it would no longer accept compostable packaging and other paper materials from the food scraps and yard trimmings it received, due to unacceptable levels of non-compostable contamination. Three-gallon compostable bags approved by the Compost Manufacturers Association were excluded from this change.
A1 Organics was neither the first nor the only U.S. composter to stop accepting compostable packaging in recent years in order to safeguard the quality of their product. Many other composters have also implemented pre-processing steps to remove compostable packaging along with contaminants. Yet, at the same time, more municipalities are launching composting systems, boosted by state laws, and more facilities are accepting compostable packaging, while the amount of composting packaging being produced is on the rise.
“The three main problems with compostable packaging are contamination, contamination and contamination,” said Neil Edgar, the executive director of the California Compost Coalition and chair of the California Organics Recycling Council’s Legislative and Environmental Affairs Committee. Edgar has been working “on the behalf of the composters” on issues related to compostable packaging for 20 years and continues to advocate for its acceptance.
A1 has since loosened its restriction slightly to also allow smaller compostable bags, but the new policy made ripples throughout the composting industry, given the company’s long history in Colorado.
Debates continue over whether and which types of compostable packaging should be accepted — and how to handle the technical processes and communication challenges linked to running successful programs. Two U.S. cities, San Francisco and Minneapolis, offer different approaches and outcomes that could help others navigate the issue.
A microcosm on the bay
While San Francisco is considered a pioneer in food waste diversion, it’s also a microcosm of the complexities of scaling up a mandatory composting system.
Here, a curbside food scrap collection program for composting, which started as a pilot program in 1996, became mandatory for residents and businesses in 2009. It has kept more than 2.5 million tons of compostable material out of landfill, according to the city, and diverts a reported 500 tons of material daily.
But directives to residents are not always consistent. As of the fall of 2023, the “What Goes Where” page on service provider Recology’s website lists “biodegradable” bags on its list of unacceptable materials (bags marked biodegradable are not likely compostable) but it makes no mention of accepting compostable plastic bags with food scraps.
“That's an error,” says Hilary Near, commercial zero waste senior coordinator in San Francisco’s Environment Department, adding that Recology did not have the city’s authorization to post that list of acceptable and unacceptable items and that the “shared” website SFRecycles.org is where all consumers should be directed. Recology declined an interview request for this story.
The labels on curbside bins clearly state that compostable products, certified by the Biodegradable Products Institute, are accepted. BPI works with producers to certify packaging to ASTM standards for compostability.
However, when the food waste collected from the city arrives at Recology’s Blossom Valley Organics North facility, it goes through mechanical processing designed to remove everything but food and plant waste.
“We're not unique in the fact that these mechanical systems can't distinguish between conventional plastic and compostable,” Near said. But, she added, numerous programs and studies have proven that residents — especially in apartments, where central collection carts can be far from their kitchens — are far more likely to follow the food-diversion mandate when they have access to compostable liners.
Plus, Near is confident any compostable plastics that are not screened out do biodegrade sufficiently at the composting facility, which uses an aerated static pile process.
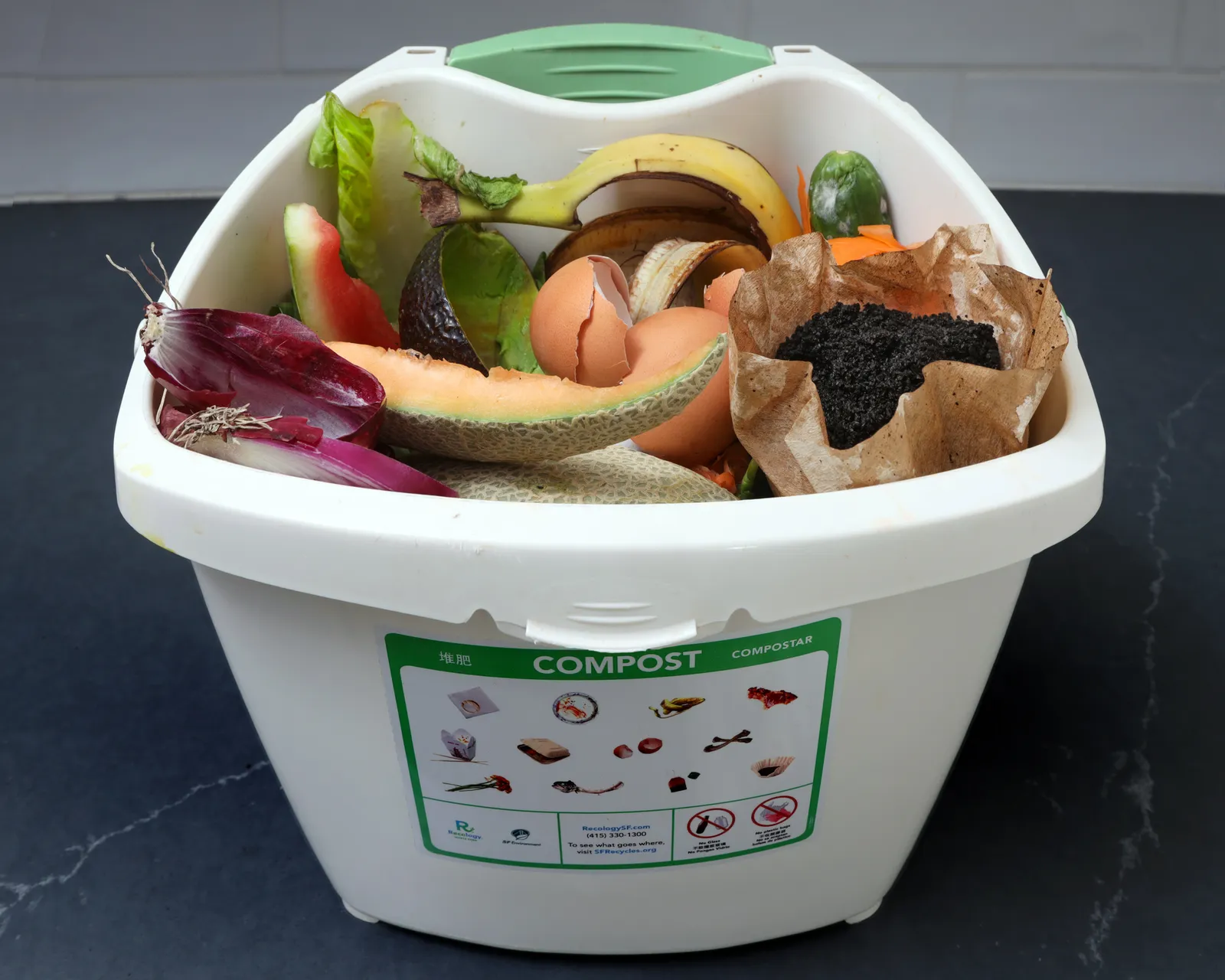
The Minneapolis approach
Two thousand miles northeast, the city of Minneapolis rolled out city-wide residential curbside organics collection in 2016. But a key difference is that this program is opt-in, with around half of residents participating. Large food-generating businesses are also required to separate organic waste.
The city’s website makes clear that the program accepts BPI-certified compostable products, though compostable liners are not explicitly listed. Haulers also manually check each cart for contamination before collection.
Organics are sent to Specialized Environmental Technologies, where Jack Duame is quality control and environmental compliance specialist. SET, which is now owned by WM, works with its customers to dissuade contamination. Their facility’s composting workflow does not include a mechanical separation early in the process that would remove compostable and non-compostable plastics alike.
“SET definitely sees compostable packaging as a necessary path towards reaching sustainability goals and getting closer to zero waste,” said Duame.
However, he added, the voluntary nature of the residential program in Minneapolis means it is likely far less contaminated than what Recology receives from curbside collection in San Francisco. Minneapolis residents who opt-in “have more of a vested interest in being a good steward and participating,” he said.
SET’s first tool in ensuring it can produce high-quality compost is to refuse to accept loads with high levels of contamination. Workers make that determination based on visual inspections. Once loads with what are deemed acceptable levels of contamination are dumped out, workers physically pull obvious contaminants that can be easily removed.
The material is not shredded before it enters SET’s aerated static piles, where it sits for 45 to 60 days in the first stage of biodegradation. This, Duame said, means contaminants are easily removed in the trommel-screening process that takes place between the first and second phase of the composting process. The second phase lasts two to six months.
Getting it right
A common concern among stakeholders — from municipalities to composters to certifiers to industry advocates — is that contamination threatens their shared goal of reducing methane emissions from organic waste and improving soil health. Reaching that goal requires that consumers receive clear guidance, feel empowered that their actions make a difference and then become advocates for waste reduction.
“There's ‘recyclable’ and what is actually being recycled and [there’s] ‘compostable’ and what is actually being composted,” said Alex Truelove, BPI’s legislation and advocacy manager. “And obviously, the extent to which we have systems to support those products is a big part of it.”
BPI conducted a survey with Closed Loop Partners’ Composting Consortium to determine how different labeling and design techniques influence consumers’ perceptions of compostable and non-compostable packaging. It found that consumer confusion about how to handle compostable packaging has negative impacts on both composting and recycling systems — nearly a third of respondents said they would put compostable packaging in recycling bins.
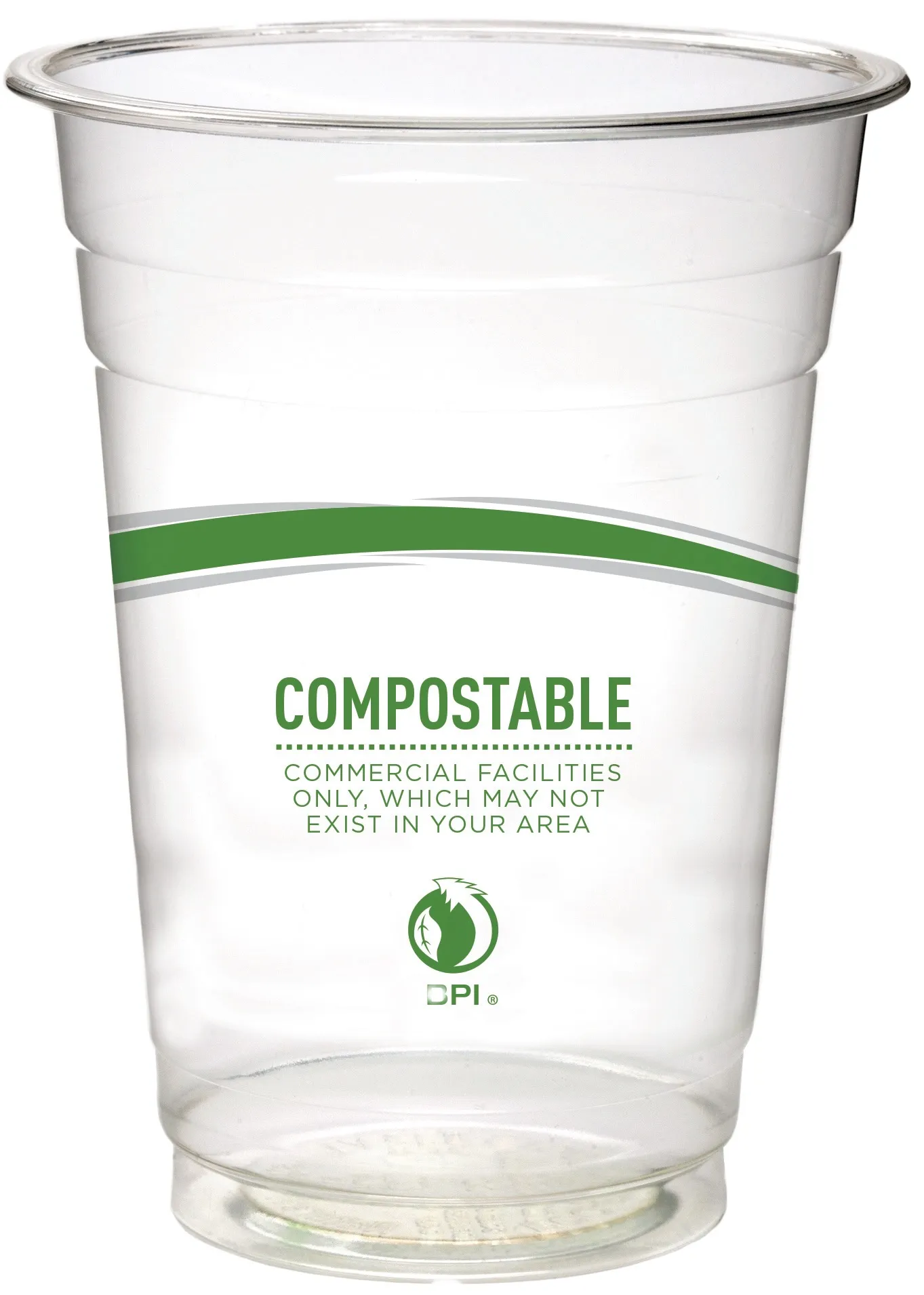
Working with the US Composting Council and other stakeholders, BPI released product labeling legislative guidelines to help policymakers advance effective “truth in labeling” laws for compostable products. And groups including BPI are advocating that compostability requirements be written into extended producer responsibility laws, while also asking the Federal Trade Commission to update compostability guidelines for environmental marketing as part of the agency’s next Green Guides update.
To date, five states — California, Washington, Minnesota, Maryland, and Colorado — have laws that govern how compostable packaging is labeled and marketed, prohibiting the use of terms such as “biodegradable” or other messaging that could confuse consumers.
“That needs to happen in the other 45 states for packaging manufacturers to be able to produce products that are meeting a similar or almost identical standard across the country. You can't have a patchwork approach,” said Edgar, who in addition to his work in California is a board member of USCC.
Grappling with inconsistent outcomes from compostable packaging while she served on the leadership team at Seattle composter Cedar Grove led Susan Thoman to found the Compost Manufacturing Alliance. “BPI does a wonderful job,” Thoman said, of ensuring that compostable material “actually does biodegrade to biomass and water versus just splintering into fragments that will be microplastics.”
But while BPI certifications are lab-based, she said composters need field-based assurance. To that end, CMA performs field testing to certify the compostability of packaging for specific types of composting environments, such as windrows, covered in-vessel and aerated static piles. CMA recently said it will no longer accept outside certifications in lieu of lab reports for its own certification process.
A1 Organics is one of CMA’s field testing partners and requires CMA certification for the compostable liners it accepts.
CMA advocated for and worked to shape Washington’s organics management law, and support Washington’s HB 1033, which passed this year and directs the state’s Department of Ecology to develop a strategy to reduce organics contamination, evaluate compostable product standards and support organic waste management. It has consulted on other state laws related to organics diversion and EPR, including in California.
At the federal level, three bills, the COMPOST Act, the Recycling and Composting Accountability Act and the Zero Food Waste Act, were reintroduced this year. Congress has not voted on them to date.
Other industry efforts include petitioning the National Organics Program to revise its current prohibition of compost generated with compostable plastics in certified-organic agriculture. This forces any composter that markets its product as certified organic by the U.S. Department of Agriculture to screen out all compostable plastics.
One sentiment that many municipal composting stakeholders share is that compostable packaging can help divert more food waste into organic recycling programs, and that because of this, it has clear value.
“We really see compostable products as a means to an end to get these desirable organic feedstocks out of landfills and into compost facilities,” said Margaret Eldridge, BPI’s certification director. “It's kind of like the tortilla chip that's used to get the guacamole to your mouth. You really want the guacamole. But the chip is an effective vehicle to get it there.”
Navigating packaging restrictions and systems
After A1 announced its restrictions on accepted materials, Eco-Cycle (a nonprofit recycler that provides organics hauling services in Colorado’s Boulder and Broomfield counties) worked to educate businesses and residents about the change.
There’s been “a lot of disappointment that compostables are no longer accepted,” said Marti Matsch, Eco-Cycle’s deputy director. “People have really become dependent upon [compostable] products, not just at restaurants, but for family picnics and community events.”
But, Matsch added, Eco-Cycle has taken this as an opportunity to “pivot our community toward reuse” with “messaging and education to help people understand that single-use disposables of any kind — whether they're recyclable or compostable — aren't always necessary.” She pointed to DeliverZero, a provider of reusable to-go packaging, as a promising model for reuse.
SF Environment is also pushing reuse and has launched a grant program that helps restaurants replace single-use items with reusable plates, glasses and silverware. For take-out, businesses in the city must use recyclable or compostable food service ware, per a 2007 ordinance.
But Neil Edgar said that while reuse is important, consumers ultimately want convenience, which means “there's a needed pathway forward for compostable packaging.”
He said the perceived failures of compostable packaging are due to a mismatch between what brand owners say consumers want and what actually happens at the end of those products’ lifecycle, with most of it being landfilled. The packaging industry, he said, “has not done much to address composter concerns primarily over labeling” while continuing to produce more products irrespective of whether they are sold into markets with infrastructure for commercial composting.
In one sign of growing attention to this area, researchers at Clemson University in South Carolina (where the Sonoco Foundation funds the Food Research Excellence for Safety & Health lab) are launching a packaging and sustainability initiative that plans to help brands test packaging compostability while also working with them to scale up compostable packaging manufacturing processes.
Rhodes Yepsen, executive director of BPI, said producers need to work with municipalities, composters and government agencies to align around common goals for designing and testing material. In his view, there is no point in companies spending “millions of dollars and years to do research and design and development” to ensure compostability, “just to have it thrown out.”