Across the globe, R&D focused on making edible packaging from materials such as seaweed is on the rise. The goal is to produce functional packaging that is fit for human consumption, while also being safe if it ends up in a compost pile or finds its way into the ocean.
Notpla — a U.K.-based sustainable packaging company that won Prince William’s Earthshot Prize in 2022 for its seaweed concept — is one of the most commonly cited examples. The company’s “Ooho” capsules, which are filled with an electrolyte drink, helped keep athletes hydrated at the 2019 London Marathon. This year, Notpla provided its plastic-free edible bubbles to the Göteborgsvarvet half marathon in Gothenburg, Sweden.
Meanwhile, Indonesia-based Evoware has a similar mission. Using seaweed, the company is creating food packaging that is safe to consume, potentially eliminating the waste that would typically arise from plastic packaging alternatives.
This innovation in edible seaweed packaging is part of a trend toward displacing plastic. While bioplastics made from materials other than seaweed are sometimes touted as a solution, some evidence has shown they can still potentially pose problems when released into the environment. Recent studies from academics in Portugal and Sweden, among others, have raised concerns about health effects when marine life and fish are exposed to certain bioplastics.
While data on edible packaging remains limited, one report from Fact.MR valued the global edible packaging market at $1.11 billion in 2023 and predicted it could grow to $4.19 billion by 2033.
The broader concept itself has also been proven in other applications. Materials that can be used as containers and are also edible by humans have long been used in the pharmaceutical industry. Pill casings are typically made using gelatin, or cellulose as a vegetarian alternative.
“The materials mainly used to make edible packaging include polysaccharides, proteins, lipids, and blends of these (composites) with appropriate surfactants, if necessary,” said Melvin Pascall, a professor of food science and technology at The Ohio State University via email.
“Polysaccharides seems to be the leading material used to make edible packaging since it includes compounds such as tapioca, carrageen, chitosan and starches from produce such as potato, sorghum, wheat, etc. Examples of proteins used to make edible packaging materials include whey protein isolate, corn zein, egg white and collagen,” wrote Pascall, who is also a member of the Food Packaging Division at the Institute of Food Technologists.
Seaweed has been a common choice for bio-based packaging innovation in recent years, thanks to its ease of cultivation in as little as six weeks. Plus, it can degrade quickly in the event that it is not consumed. By using seaweed to replace cellophane, or other kinds of hard-to-recycle plastic packaging, companies are tackling the low-hanging fruit for keeping packaging from disposal.
"The packaging basically will dissolve quickly ... especially in warm water," said Ahmad Ikhsan Muharram, marketing communications manager at Evoware. "It will not leave any residue or waste." One application for Evoware’s seaweed-based packaging is a noodle soup seasoning sachet that would typically be discarded once emptied. Instead, the entire dissolvable and edible sachet could be added to the soup.
In addition to edible sachets, companies are producing edible straws. Evoware has made a straw from rice. "It actually feels like [dry] pasta,” said Muharram.
Barcelona-based edible straw company Sorbos uses sugar and cornstarch to make its flavored straws, which are gluten free but do contain bovine gelatin. They can stay rigid for around 40 minutes in a cold drink. Carnival Cruise Line is one of the company’s biggest partners.
"Paper straws and plastic straws were actually getting caught in their pump for their swimming pools," said Scott Bell, the company’s marketing director and head of European sales. "Sorbos mitigates any of that risk for them."
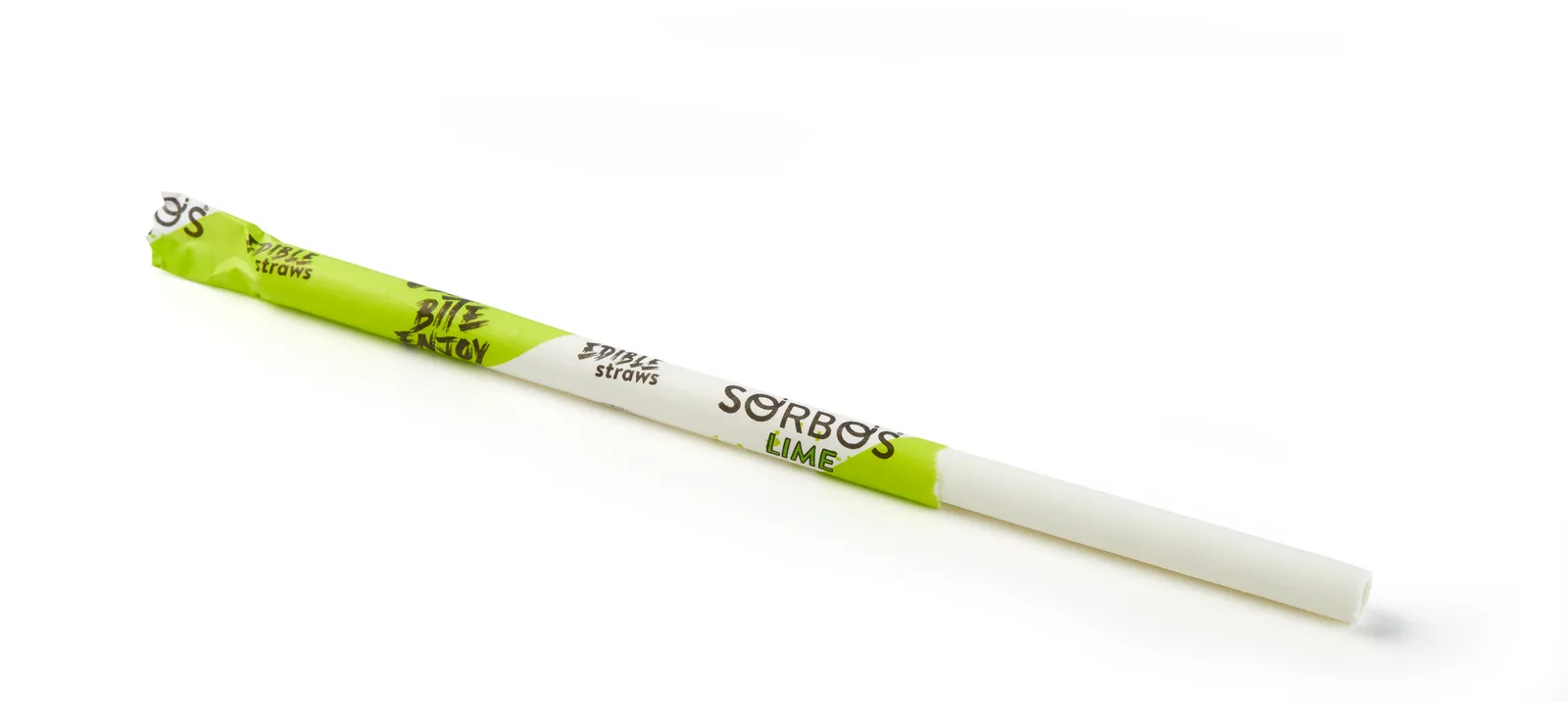
Meanwhile, brewers are using rings made from wheat and barley to hold cans together. While they may not taste great, they can be consumed. This can reduce the harm to ocean life from plastic can carrier rings.
The team at Forest & Whale, a multidisciplinary design practice focused on circular systems, has developed a salad container made from wheat husk that has edible components. The project is still in the prototype stage.
“Manufacturing the wheat husk containers requires very high quantities (because the metal molds are complicated), so the investment requirements are equally high, therefore we are looking for partners that can ensure large quantities of regular use before going into production,” said Gustavo Maggio co-founder and creative director, via email.
Similarly, some challenges connected with scaling remain for seaweed-based edible packaging products. Companies like Evoware are currently limited by production.
“It’s still in the developing stages,” said Muharram. "When [potential clients] talk about the quantity required, sometimes we cannot fulfill that need."
The logistics of manufacturing will need to align for edible packaging to displace plastic in a meaningful way. Plus, edible packaging must be protected from contamination when stored or in transit, prior to reaching the customer who will consume it. Where plastic packaging is replaced with an edible wrap or container, companies must consider what surfaces or items the products encounter.
“This need to protect the package tends to increase the cost of commodities using edible packaging,” said Pascall.