More brands are switching away from plastic packaging to fulfill sustainability commitments — fueling innovation and market opportunities for molded fiber product manufacturers to fill the void, according to speakers at the International Molded Fiber Association's annual conference in Carlsbad, California, last week.
"We get a lot of customers that come to us and say, 'We want to make this plastic transition,'" and moving into molded fiber often fits the bill, said Nick Palumbo, North American technical sales manager for the fiber division at equipment supplier Kiefel Technologies.
Molded fiber, or molded pulp, packaging competes primarily with expanded polystyrene and thermoformed plastic, said John Sherwin, co-director of custom research at The Freedonia Group.
Although "you're seeing a lot of larger companies pushing away from plastics," those materials are "deeply entrenched in our society, making it difficult to replace," due to performance benefits and their light weight, Sherwin said. But recent challenges to plastic use have "made molded fiber the choice to replace it," he said.
Factors that have caused big molded fiber market changes since 2015 include increased environmental awareness, corporate sustainability goals, regulatory pressure and technological advancements resulting in improved performance of alternative materials, Sherwin said.
Growth markets
While the molded fiber market value hovered around $1 billion in 2014 and 2015, Freedonia has charted a steeper growth curve since then and predicts expansion to more than $4 billion by 2030.
Protective and secondary packaging dominate molded fiber demand
Demand continues to increase among food service customers, with 10% growth in that sector expected each year until 2028, when the market will be worth $2.3 billion. Of the food service demand, service ware and trays comprise the biggest share, followed by cups, tubs and lids. Freedonia expects the fastest growth in the food service category to occur in food and beverage cups.
The growth of molded fiber food service disposables in the U.S. has aligned with the popularity of food takeout and delivery; demand for clamshells and two-piece containers is strong, Sherwin said. In Canada and Europe, stricter regulations on foam and single-use plastic packaging have created an opening in the market for molded fiber.
Improvements in non-PFAS coatings will further boost growth for food-safe molded fiber disposables, Sherwin said. He noted the recent announcement of graphene oxide as a potential food-safe PFAS alternative as an example.
"The better the coatings, the more options that you could get into in terms of market penetration. And those kinds of innovations will drive critical growth," Sherwin said.
While the protective packaging market is more mature, it also presents a significant opportunity for growth, Sherwin said. The push for making e-commerce more sustainable is one area that holds potential.
For instance, Amazon's and other companies' efforts to ship products in their own containers has ballooned from less than 5% of products shipped in 2018 to nearly 15% by 2023 and a projection of nearly 35% by 2033. Tapping into this market could boost molded fiber sales as consumer product manufacturers look to improve packaging durability to meet the rigors of SIOC.
And while gains in egg cartons had stagnated or decreased slightly, the sector is getting new life as plastic replacement proliferates, Sherwin said. More demand for molded fiber egg cartons has occurred as egg suppliers shift away from expanded polystyrene egg cartons; the opportunities are greatest among egg suppliers aiming for an environmentally conscious image, such as for free-range options.
Other applications where molded fiber could take share from plastic include multipack beverage carrier rings. "Plastic beverage carriers probably have the worst reputation of all packaging products," Sherwin said.
Opportunity is also ripe in emerging spaces such as coffee pods. Innovating molded fiber for new product sectors as well as adapting existing products is key, Sherwin suggested.
Working to develop products that are more aesthetically appealing to consumers is the next step toward growth, Sherwin said.
Hurdles to expansion
Building on the theme of innovation, IMFA Executive Chairman Gary Visser said that the "conventional [molded fiber] machines that have been around for decades have made leaps and bounds" in terms of production capacity. But further technological advances are needed.
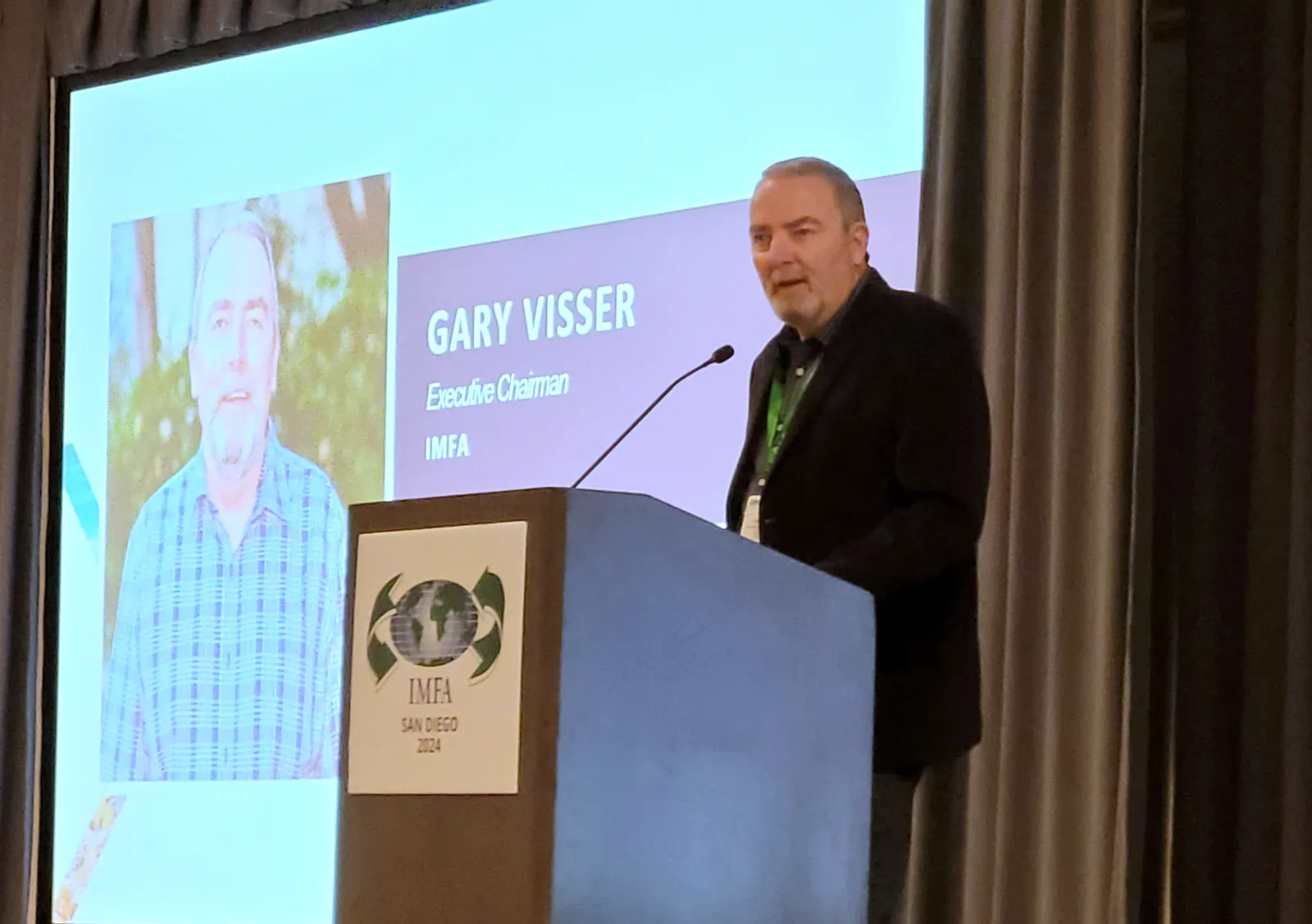
"We're competing with a substrate ... that for the same amount of real estate will be putting out 10 times what we put out," Visser said, making a comparison to plastic packaging production.
Industry participants are also hoping that technological advancements can address another key sticking point: energy consumption. "There is no doubt that there are energy challenges in the industry," Visser said, meaning the amount of power needed to run the heating equipment that dries wet molded fiber products after they're made.
Innovation must also occur in alignment with existing and upcoming regulations. For instance, speakers pointed to the need to comply with food-contact regulations without compromising performance, such as when seeking alternatives to PFAS barriers.
Another challenge is that the feedstocks used to manufacture molded fiber packaging are shifting. Recovered paper is still a significant source of fiber for the industry, but its share has dropped slightly, said Bill Moore, president of consulting firm Moore & Associates. The total supply of paper available for recovery in the U.S. is declining as demand for recovered paper is increasing, he said.
For example, newspaper is a primary grade used in molded fiber production, especially for egg cartons, produce packaging and food service products, he said. However, Moore said the sharp decline in newspaper readership, and consequently printing, is resulting in a dwindling supply: The U.S. has seen a staggering 90% decline in newspaper consumption in the last 25 years.
Corrugated is another primary grade and is typically used for protective packaging as well as some produce applications. A third feedstock is polycoated cup and plate stock, which typically goes back into white plates and similar products.
In 2023, the U.S. recovered paper supply in the newspaper category was only 1.6 million tons, compared with 33 million tons for corrugated, Moore said. The use of double-lined kraft has risen significantly in the last five years, he said, and the main source is corrugated box converting plants.
“The corrugated grades are becoming more and more used,” Moore said. But pricing and supply volatility have been factors since the pandemic. Box use spiked with the e-commerce boom during the early pandemic and then fell into the “corrugated box recession” in the following years, reaching its bottom last year.
The search is on for alternative fiber sources as well, Moore said, pointing to bamboo and bagasse, among others. But recovered paper alternatives can be more difficult to use, he cautioned.