While market growth emerged as an underlying theme at the International Molded Fiber Association’s annual conference from Sept. 11-13, innovation became the frequently repeated strategy for accelerating that trend.
Innovating by upgrading existing molded fiber products as well as entering new territory, such as coffee pods, is a key strategy for market expansion, said John Sherwin, co-director of custom research at The Freedonia Group. And exploring viable new barriers as alternatives to PFAS will further boost growth for food-safe molded fiber disposables, he said.
Jan Ridderman, sales manager at Inmaco Solutions, said he’d seen the industry change during his last two decades making machinery. As more customers to turn molded fiber solutions to meet sustainability goals, Ridderman said the manufacturing equipment also is changing to keep up with the industry’s innovations.
Automation advancements
Nick Palumbo, North American technical sales manager for the fiber division at equipment supplier Kiefel Technologies, offered an overview of recent technical advancements in molded fiber automation.
For one, he described changes in trimming during the manufacturing process that reduce tooling costs and offer higher precision.
“We’ve seen that multi-stage trimming can really help increase output. It will allow you to do multiple cuts on the same article,” he said. “Then we’re looking also into laser trimming as well — currently being developed.”
Examining how best to configure machines for process optimization also presents opportunities, he said.
“We've done a few different, newer things, where we're actually feeding multiple thermoformers, or molded fiber machines, into one set of automation tools,” Palumbo said. “You can increase your automation usage so you're not having your automation sit unutilized. It'll lower your labor costs and reduce the footprint of having automation on individual machines — you have them in a cell.”
In addition, digitizing via a human-machine interface, which operates similarly to a standard tablet, helps by giving live feedback about operations data. This HMI boosts precision and allows operators to get ahead of potential issues, Palumbo said.
Pre-pressing, or cold-pressing, packaging before it goes into the hot press also has benefits, according to Palumbo. “It allows you to pre-form your parts, so adding undercuts or some stacking features ... can be achieved better by getting more moisture out before you go to hot press,” he said.
Modern equipment also has made moves toward greater energy efficiency, speakers said, addressing a known industry challenge with wet molded fiber heating equipment’s substantial energy consumption.
Drying out
PulPac highlighted their dry molded fiber innovation, which they tout as being more sustainable than the wet molded fiber manufacturing process.
Having only launched as a company in 2018, “it's a young technology,” and PulPac continues to perform R&D on it — both to optimize machinery and production as well as to identify new end markets for users — said Chief Commerical Officer Sanna Fager.
PulPac licenses its technology to users, and up until now it hasn’t had a prominent U.S. presence. But just last week, PulPac announced that Dart became the first North America-based licensee for its Scala production technology, which is about half the factory footprint size as Modula, PulPac’s separate technology that already was present in North America.
Equipment supplier Curt G. Joa already had a relationship with PulPac, as did Graphic Packaging International, which gained the relationship via its 2021 acquisition of Belgium-based AR Packaging, a company that had licensed PulPac’s technology.
Fager described the dry molded fiber manufacturing process in which defibrated pulp is turned into a web-like material, barriers are applied, then heat and pressure are applied in a standard plate press to form the material into a product.
While R&D is ongoing, the “challenge here is, how do we grow the market as quick as possible” and achieve scale, Fager said. “Our business model is for rapid scaling.”
Ring of fiber
Molded fiber’s push into new end markets is a key theme that The Freedonia Group flagged as a driver for growth earlier in the conference. Multipack beverage carriers are a top category that fits under that umbrella, according to the research firm.
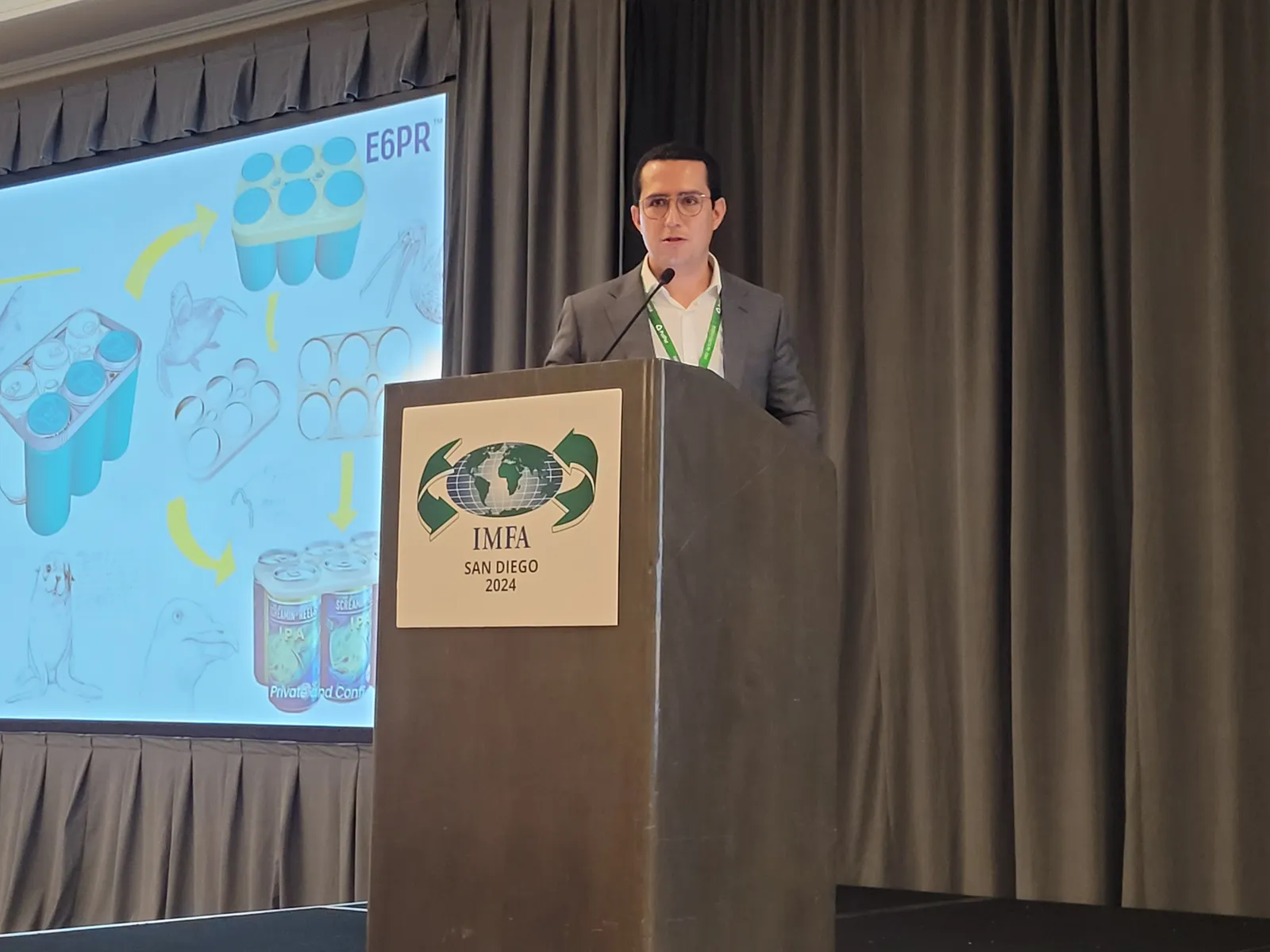
Francisco García, co-founder and chief operating officer at E6PR, detailed how his company was a trailblazer in developing molded fiber rings to replace plastic rings on beverage multipacks.
“I want to share with you the potential of molded fiber parts going into new markets,” García said. “There are still new markets we see every day.”
E6PR worked with Florida-based SaltWater Brewery for a couple years to design the molded fiber carriers. Numerous rounds of testing during R&D prompted the company to tweak the design to be more moisture resistant and durable under the rigors that ring carriers face.
Going to market after years of work “was a big milestone for the market and the industry,” García said. “The concept was good and the customer was willing to pay more.”
But the product price has come down to nearly reach parity with plastic rings as E6PR has scaled. That’s expected to draw in even more customers.