LanzaTech's biotechnology laboratories in the Chicago suburb of Skokie, Illinois, resemble some of the others inside its home at the Illinois Science + Technology Park, where tenants' work skews heavily toward life sciences, healthcare, pharmaceuticals and materials science. But LanzaTech's laboratory is advancing an initiative that many people wouldn't expect: plastic packaging made from air pollution.
LanzaTech helps other companies reduce their carbon footprints by using their own pollution as a feedstock to create fuel or plastic products. This mitigates the need to tap into raw material resources, like fossil fuels, to make new products, and it captures harmful emissions that otherwise would be released into the atmosphere. Often the gases are captured from industrial facilities such as steel mills; gases from customers’ own facilities or municipal solid waste also are harnessed. The end product is used to make ethanol, which commonly is motor vehicle fuel but also can be utilized as a building block for plastics, especially PET.
The company’s partners to create products from carbon emissions include H&M for making polyester clothing, Coty for making ethanol used in fragrances and Twelve to produce polypropylene for a variety of purposes. A partnership with L’Oreal and Total resulted in what partners call the first shampoo bottle made from recycled carbon emissions. It is also working with Plastipak to produce what the partners call the "world's first" PET resin made from carbon emissions that is suitable for food-grade and non-food packaging.
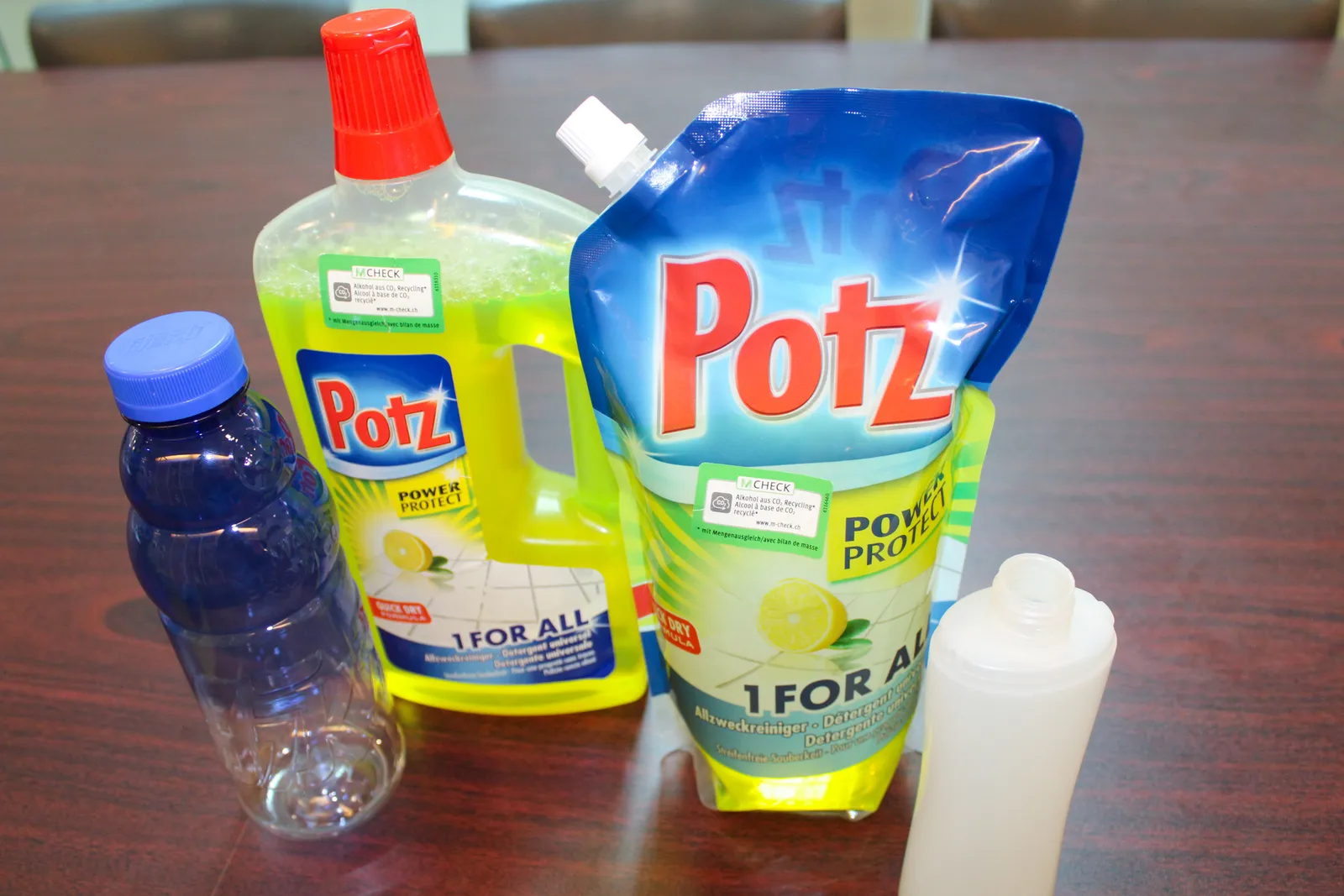
One of the most widely distributed products already on the market that LanzaTech contributed to is Potz household cleaner — both the packaging and its contents — which is available at grocery and drug stores in parts of Europe.
"What's super exciting about these products is the cleaning reagent itself is made from ethanol, but also the ethanol is the basis” for the plastic packaging, said Michael Köpke, LanzaTech's chief innovation officer.
Currently, LanzaTech’s transformed carbon component comprises about 30% of most of these packaging end products, “and we're also working on a route to get the other 70%,” said Kit McDonnell, LanzaTech communications director. This is because the company already has downstream partners who convert the ethanol produced at client facilities using LanzaTech’s technology into monoethylene glycol (MEG), an intermediate component that constitutes about 30% of PET. But the other 70% of PET is comprised of purified terephthalic acid (PTA), and LanzaTech doesn’t yet have a full commercial-scale supply chain for that component. However, the company is “working on establishing the necessary partners for converting ethanol into PTA to make 100% carbon emissions derived PET.”
The heart of the company’s multi-step process involves billions of proprietary bacteria feeding on air pollution, and the resulting byproducts are used to make ethanol and ultimately plastic products such as bottles or jugs.
"We are really focused on making molecules that are chemical intermediates to underpin how you make pretty much anything that's got a hydrocarbon in it," McDonnell said. "You can make so many different things, because carbon is in everything."
LanzaTech started up three commercial-scale production units since 2018 that each have the capacity to produce 50,000 metric tons of product per year. By year’s end, it plans for three more units to become operational, bringing total production to 300,000 metric tons per year. All six of the units are located at partner facilities, as LanzaTech’s Illinois facility is exclusively dedicated to R&D.
While some circles aim to eliminate plastic packaging altogether over environmental concerns, plastics still are necessary in modern society, including as packaging to ensure a product’s sterility and safety, McDonnell said. Therefore, LanzaTech strives to develop plastics that keep already-obtained carbon resources in circulation.
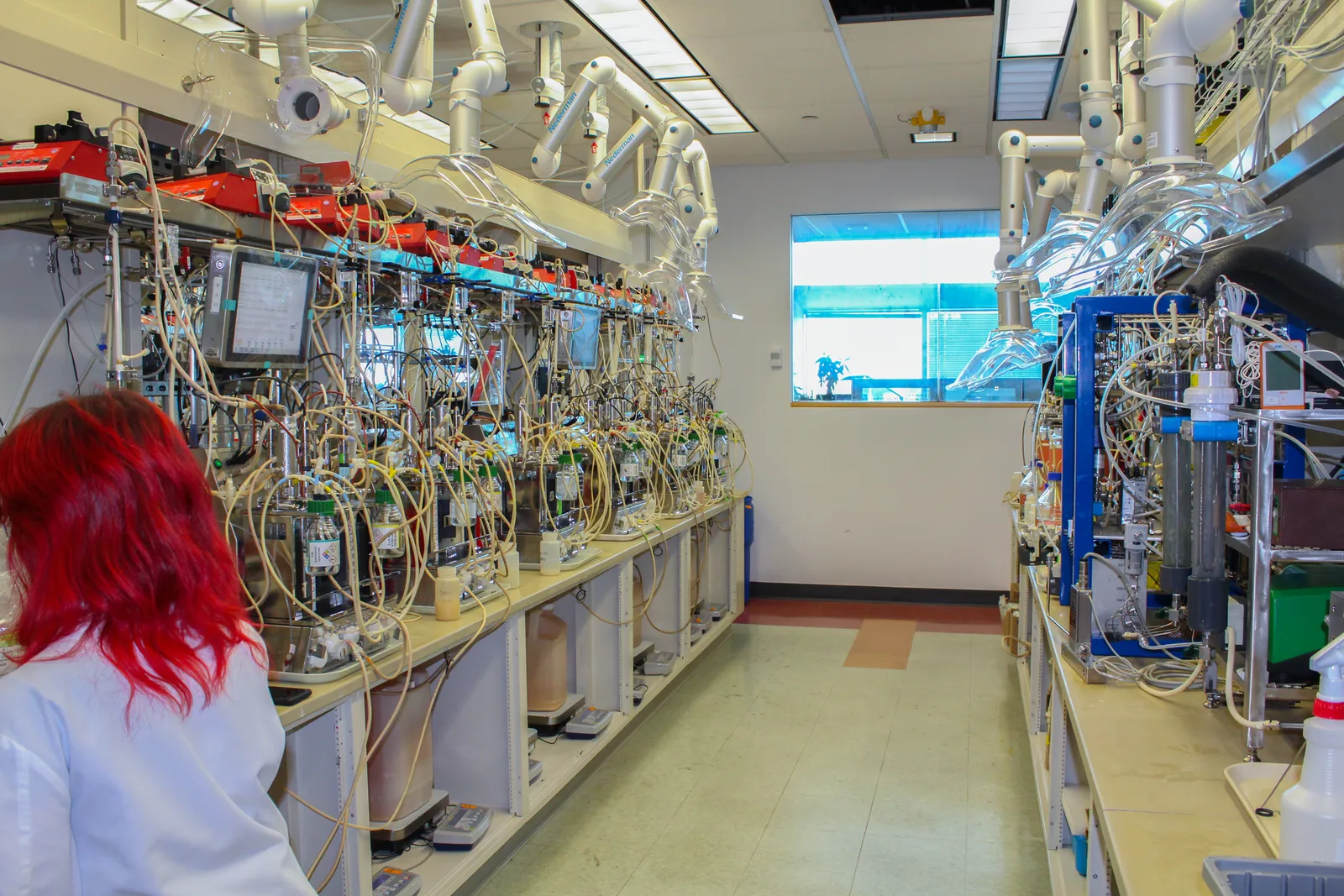
‘Like brewing beer’
LanzaTech's flagship R&D work rests in its fermentation process, or its method to break down the captured emissions. Scientists feed the gases found in emissions to bacteria, or microbes, causing a fermentation-like reaction. The resulting byproducts are used to create ethanol, which can be used as-is or as a base for other new products like plastic packaging.
The pollution transformation technique uses different elements than traditional fermentation to achieve the end result, but the bacteria reportedly are still as safe as conventional yeast.
“You can imagine it a little bit like brewing beer. But instead of sugars we use gases, and instead of yeast we have specialized microbes," Köpke said. “We use fermentation to make ethanol, but we also develop capabilities to make other molecules.”
Beer brewing typically uses batch fermentation, in which a solution sits for a period of time while fermenting and then the beverage is reaped while the solid materials are discarded. But LanzaTech uses continuous fermentation, in which gases constantly are pumped into the liquid mixture, microbes constantly divide and renew themselves and product is continuously harvested for about 300 days.
Employees precisely measure the amount of gases added to the mix and the amount of product gathered at the end. Most of the water is recycled, meaning "in addition to optimizing the bioreactors to be very energy efficient, we also optimize the process to be very resource efficient," Köpke said. "The motivation for us, of course, is having a circular carbon economy.”
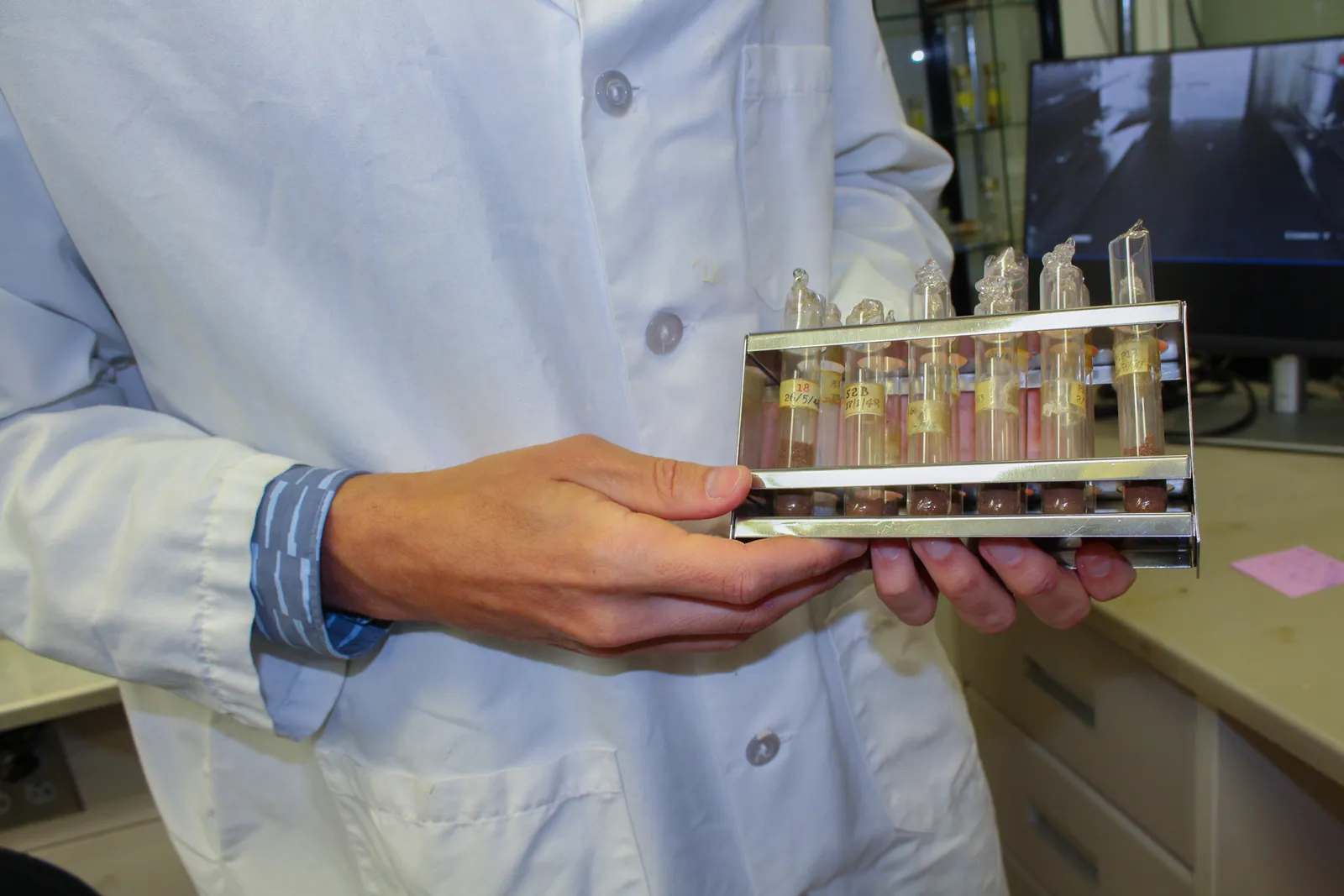
LanzaTech uses anaerobic bacteria that metabolize similarly to some of Earth's earliest microbes that gobbled up carbon dioxide, according to Köpke. The microbes are commonly found in soil, animals and humans, and LanzaTech's version comes from rabbit feces.
Over its 18 years of business, LanzaTech has genetically altered the bacteria to create its own strain that is more streamlined and productive.
"We optimized and trained that microbe to be very efficient at eating those gases and making products," Köpke said. "We've also developed genetic engineering tools where we can now bring in new pathways and functions into the microbes, so that allows us to reprogram it to make other molecules for various different products."
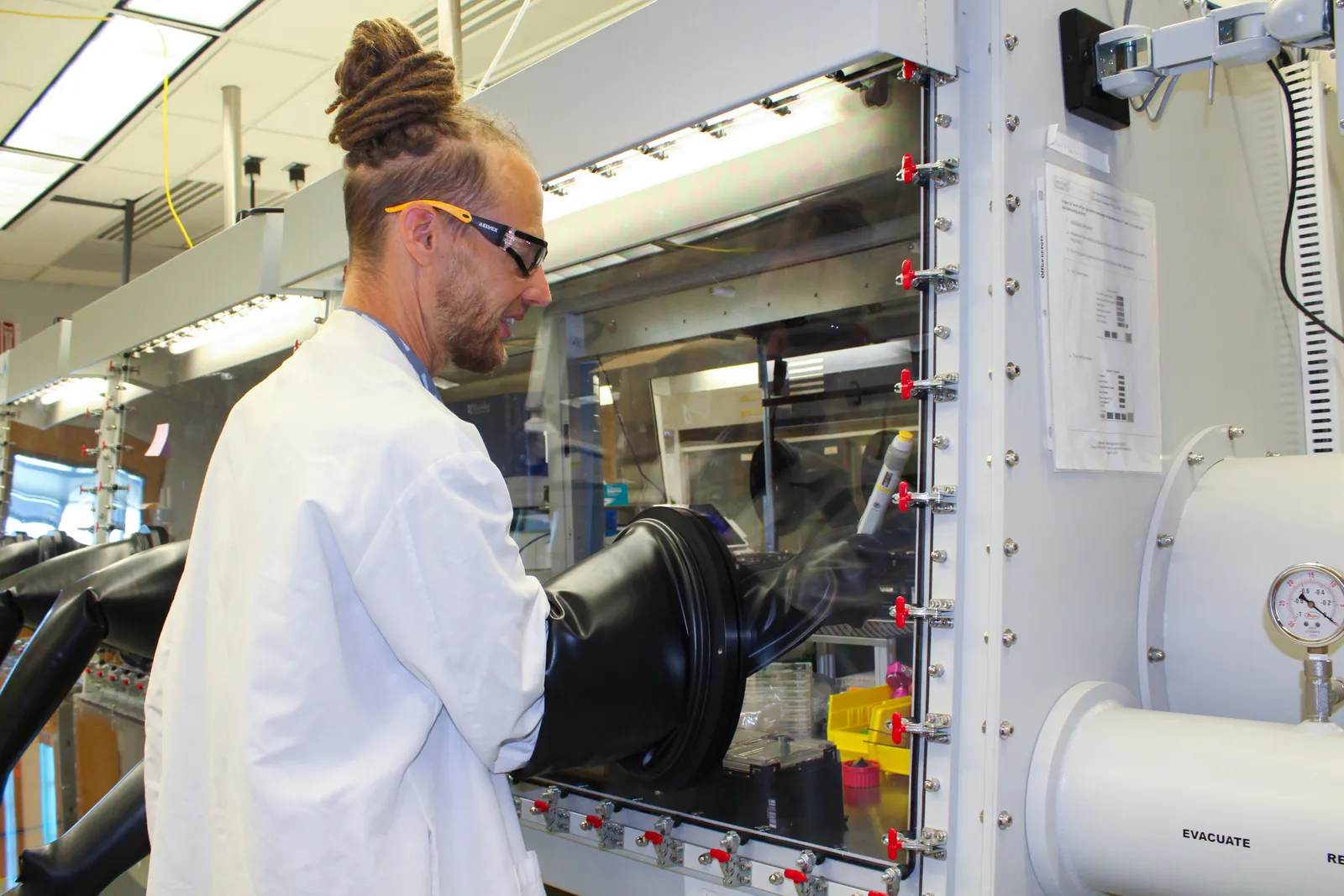
It's a gas
Large tanks of feedstock gases sit outside the Illinois R&D building, and labeled pipes route the gases inside to LanzaTech's laboratories. Scientists can apply the gases — carbon monoxide, carbon dioxide, hydrogen and nitrogen — separately or in combinations to influence the bacteria's consumption patterns and productivity.
These gases in the lab simulate the emissions produced at customers’ industrial sites. The system flexibility allows LanzaTech to cater the process to each individual customer’s emissions blend.
"If you think about a steel mill's gases, it's very rich, for example, in carbon monoxide. That carbon monoxide would be flared into the atmosphere and will become CO2" if not captured, but LanzaTech’s system instead captures those gases for reuse, Köpke said.
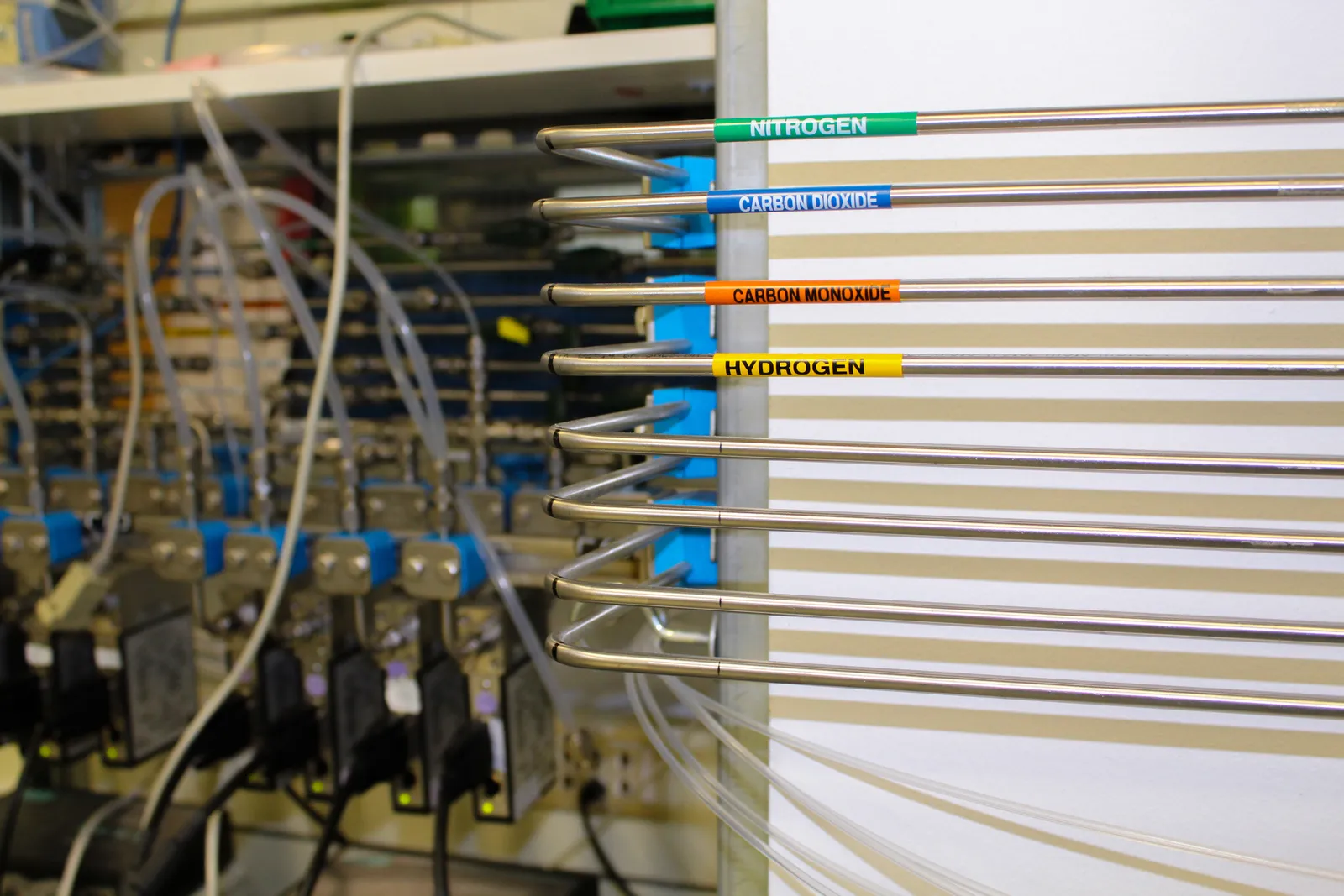
Employees at the Illinois facility combine the gases and microbes in bioreactors. The equipment agitates the solution to speed up the microbes' gas munching and transformation to an end product. LanzaTech has about 100 small, tabletop bioreactors across its four floors of laboratories, in addition to commercial-scale versions that stretch from floor to ceiling — or even to another floor.
The bioreactors have “stirrers, which make the turbulence, but if you want to scale this up to millions of liters in size, that would take a lot of energy," Köpke said. The approximately 350 lab workers and engineers have tweaked the process to make it "very energy efficient — that was a big part of the development," he added.
Some of the genetic engineering work is blossoming into a means to cut out certain intermediate plastic-making steps, which Köpke said improves the process’ carbon balance. One example is eliminating the separate process for making monoethylene glycol, an essential component of many plastics.
"In the future, we imagine a process where we can make monoethylene glycol directly at the microbe [during] the fermentation," Köpke said.
Researchers analyze the scores of data they obtain from the experiments — with assistance from AI — to continually hone the emissions transformation technique and further optimize the process to get higher product yields.
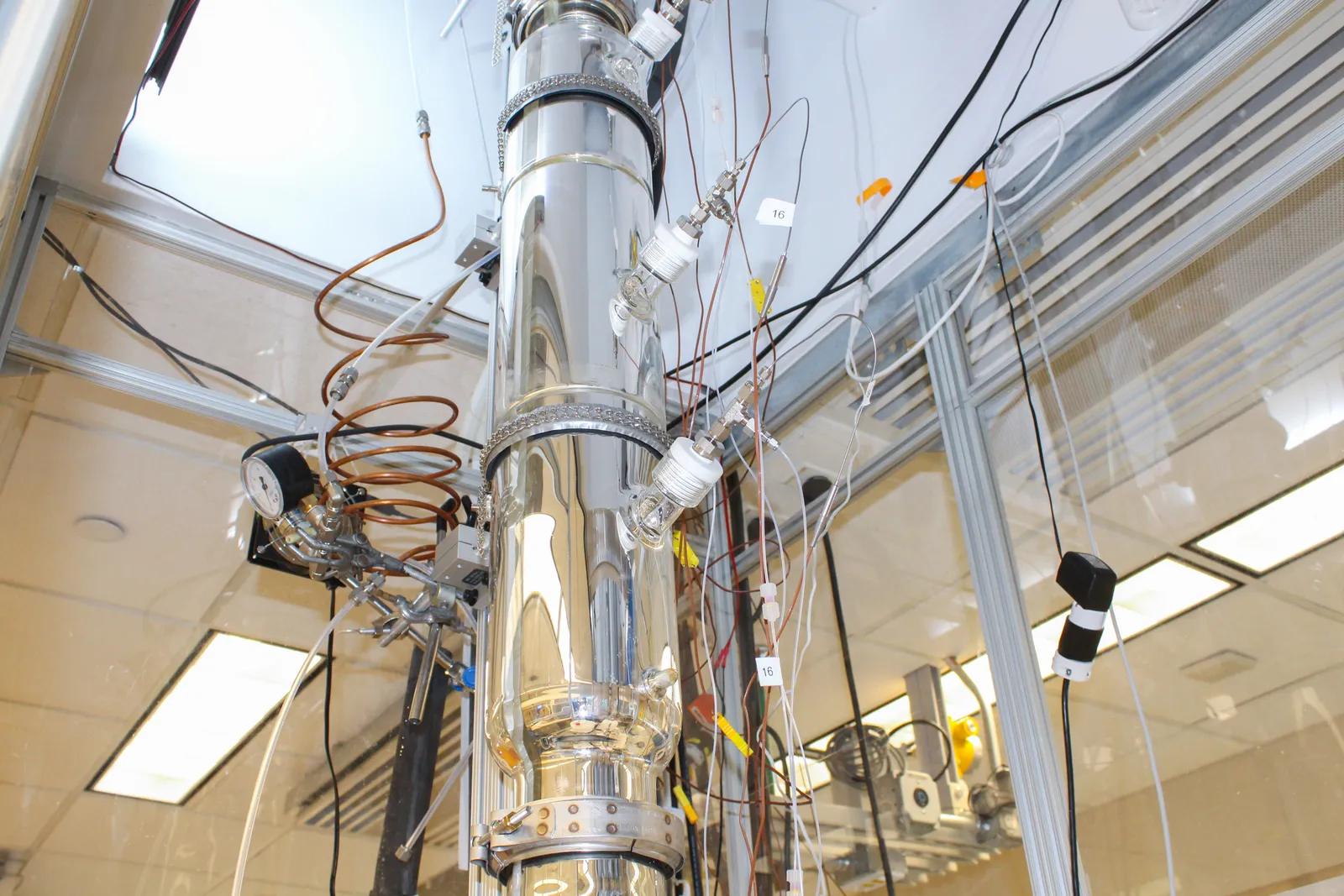
From lab to life
LanzaTech prides itself on innovating at multiple points of the value chain, from emissions feedstocks on the front end to various molecules for customer products on the back end.
After harvesting the microbes’ byproduct and sending it to be converted into ethanol, the plastic production process resembles other conventional methods. LanzaTech’s product ends up in resin pellets, which are used to manufacture new end products including plastic packaging.
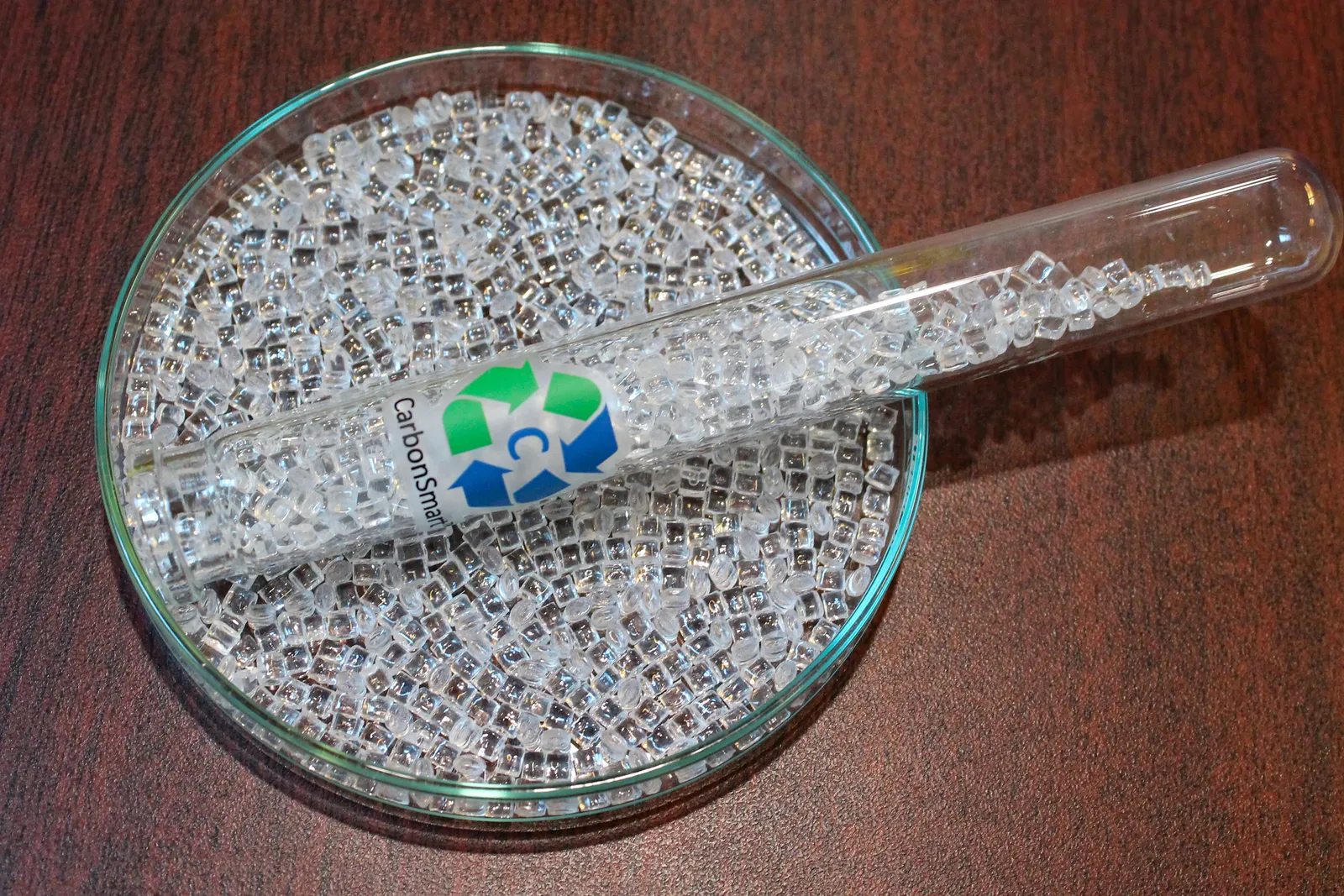
In addition to cutting out steps to make MEG directly at the microbe, LanzaTech’s future work involves advancing direct air capture technology that extracts emissions directly from the atmosphere at any location rather than carrying out carbon capture at the emissions point, such as an industrial facility. Integrating that capture capability with the existing technology could further expand the system’s flexibility and relevance to a multitude of packaging and other applications.
And what happens if feedstock emissions were to become scarce amid ongoing global decarbonization efforts?
“Certainly that would be great for society,” Köpke said. “For the next couple of decades, we're still seeing that there's emissions, and we really need to try to use as much carbon as we have.”